The Titanic’s engine project felt never quite finished for me. Even though she looked great, she did not meet one of my main criteria for success for this project, namely to run by herself on air. I tried many things, such as sanding, more or less lubrication, different brands of PLA, different valve timings and so on but I never got her to run smoothly on all four cylinders. In my search for possible solutions, I figured that one last resort would be to scale the entire engine up by a certain factor. My tolerances would stay the same, but much more air could get used to generate force to overcome friction. This turned out to be the right assumption. After printing the first cylinder at 200%, which immediatley ran without a hiccup just after assembly, I was confident that the engine would work as a whole as well.
My small airbrush compressor was by far not powerful enough to get this model going. Therefore I resorted to my vacuum cleaner. And instead of hooking the up to the inlet as in my previous air pressure engines, I connected the vacuum to the outlet. To control the speed of the engine, I had to design a pressure reducer. For this, I choose to design a tube with hundreds of small holes, which could get blocked by an overlaying piece that rotates to vary the number of blocked holes. This proved to be extremely effective and it is great fun to rev the Titanic’s engine
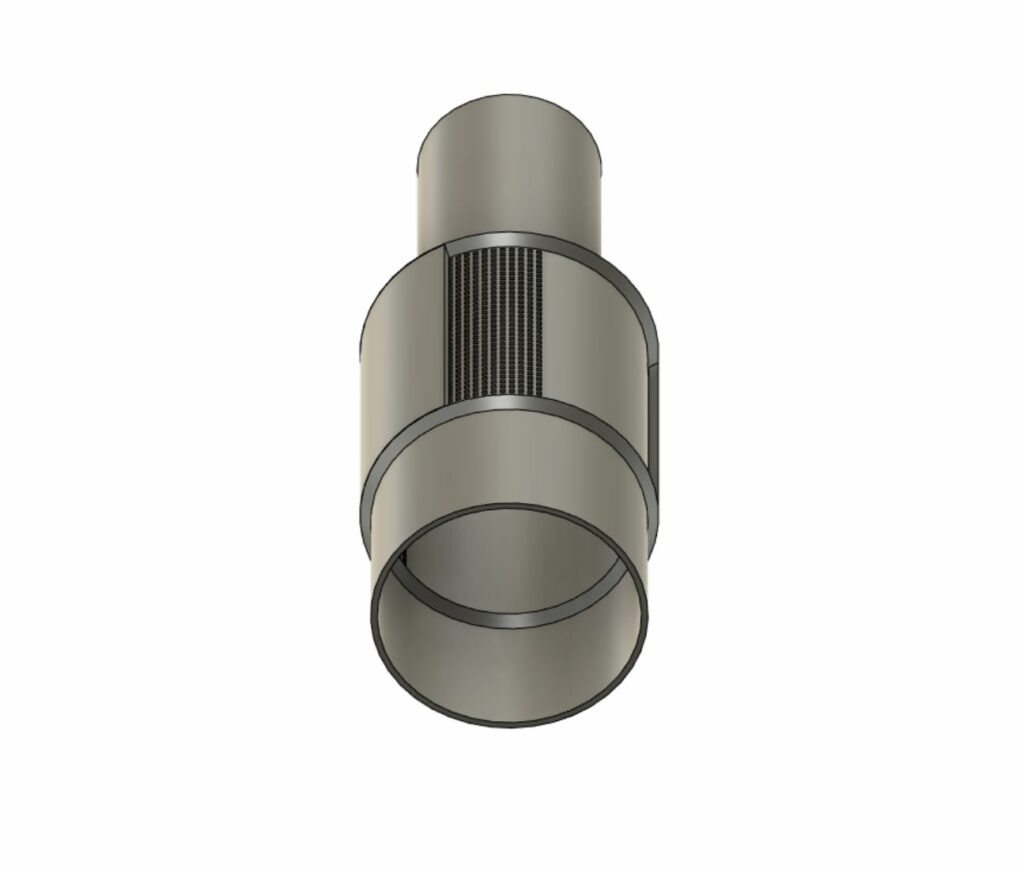
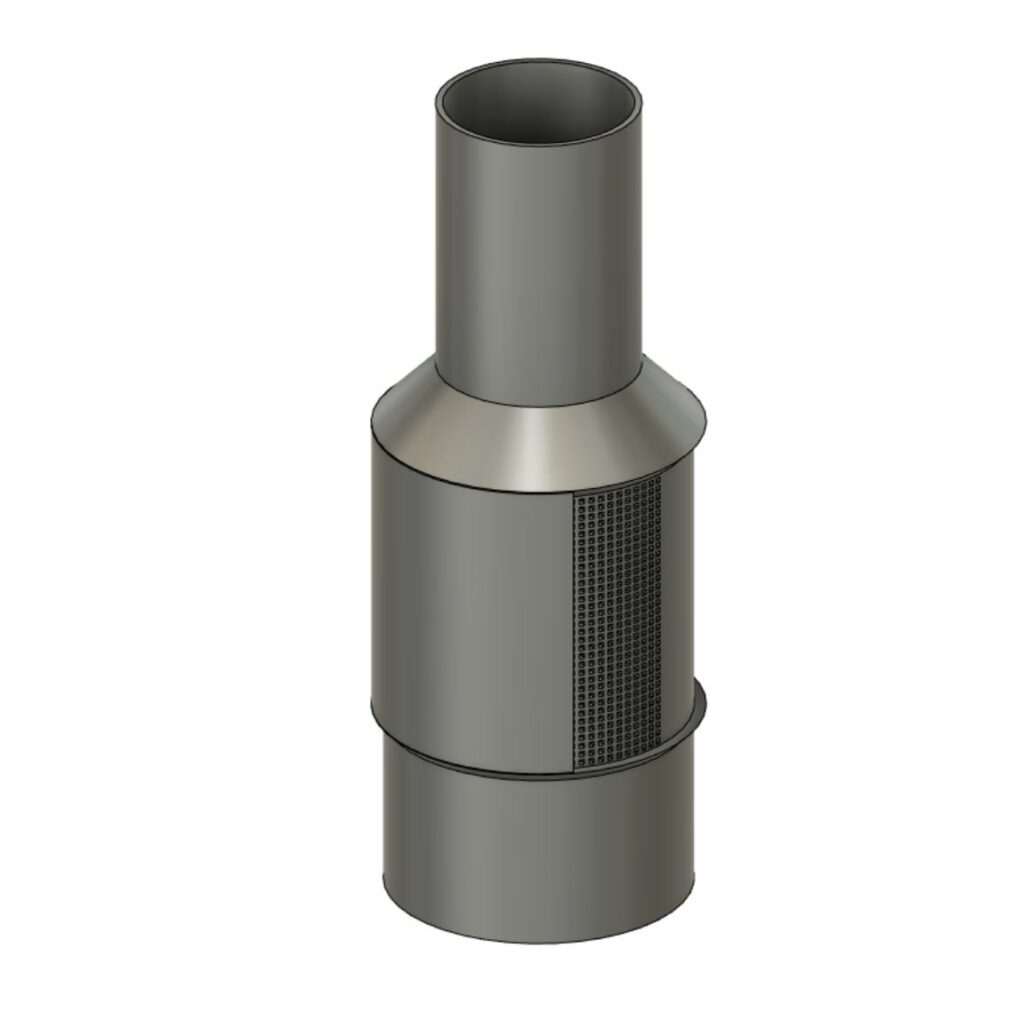
To add something for the engine to move, I decided to model one of the outboard screws of the Titanic as well. This was quite fun since I haven’t modeled such a complex organic shape as the propeller blades before. I connected them in the same way to the hub as they got connected on the real ship
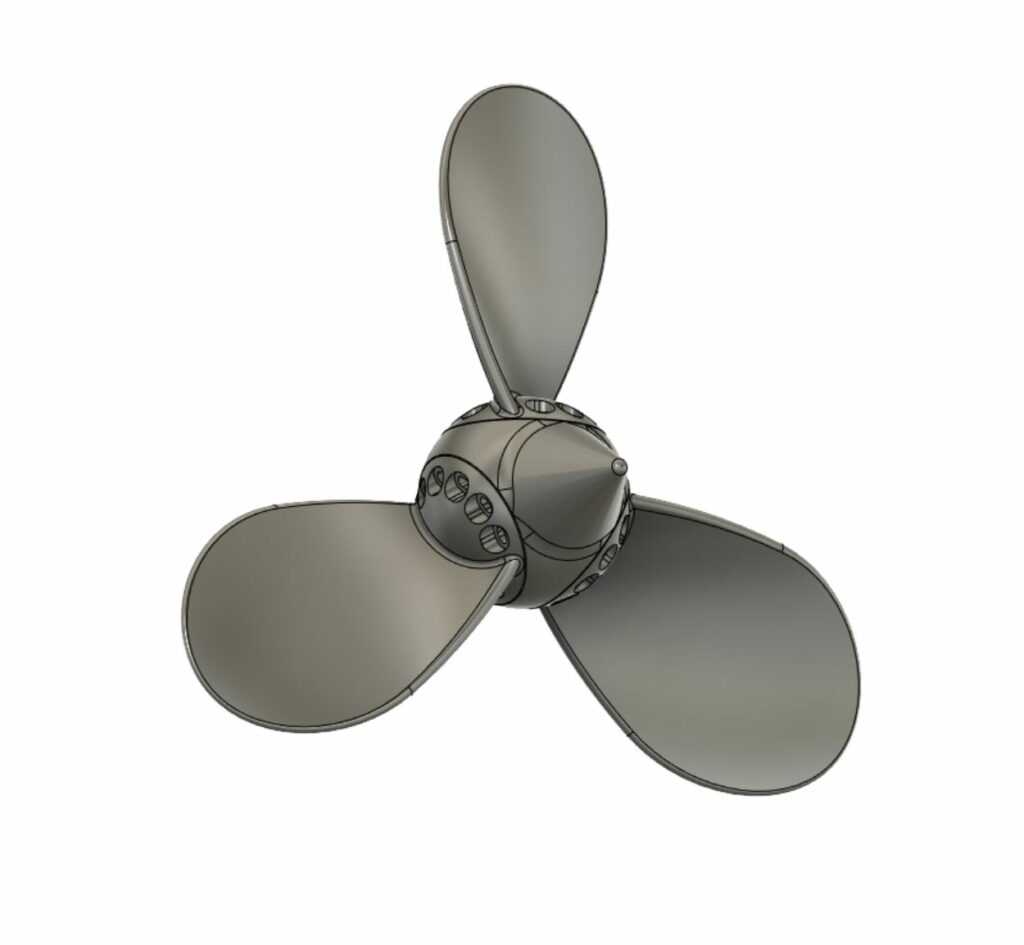
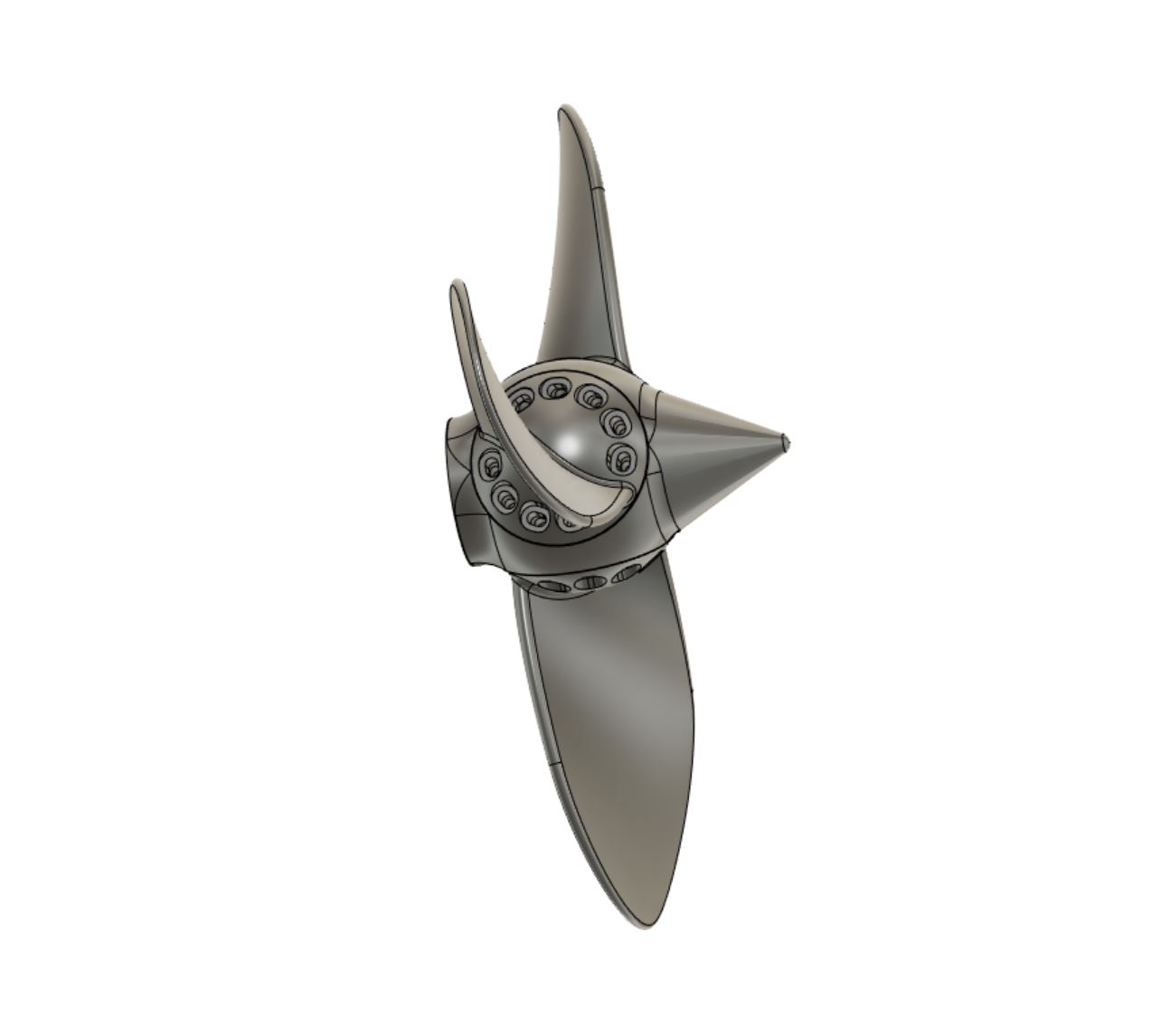
One thing that did not work well when scaled up were the eccentric valve timing disks. For my smaller builds, they were simply concentric rings that did produce some friction, but negligible due to their overall size. When scaled up however, eight of them produced so much friction that the engine would barely turn over. I experimented with different ball bearings but came to the conclusion that adding ball bearing balls into my 3D printed parts would take less of a hit on the overall look and would work absolutely perfect.
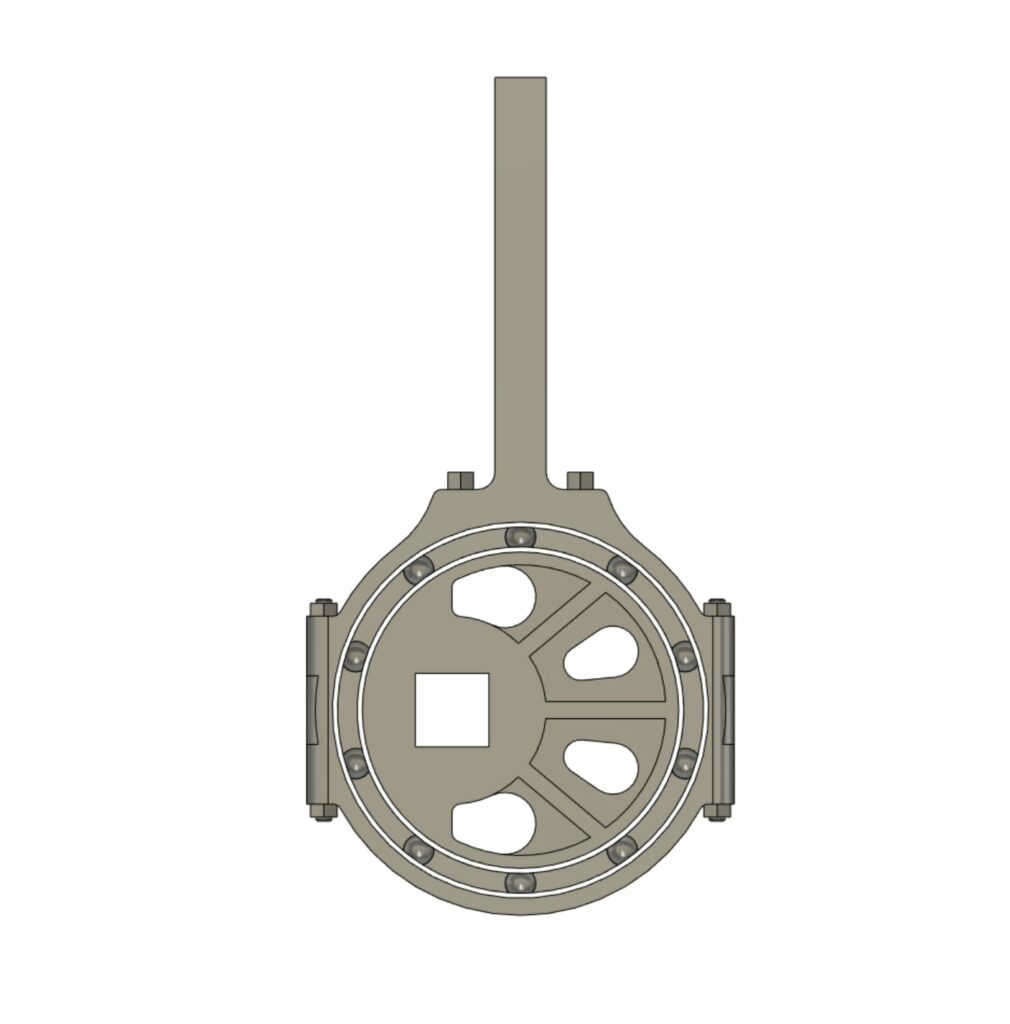
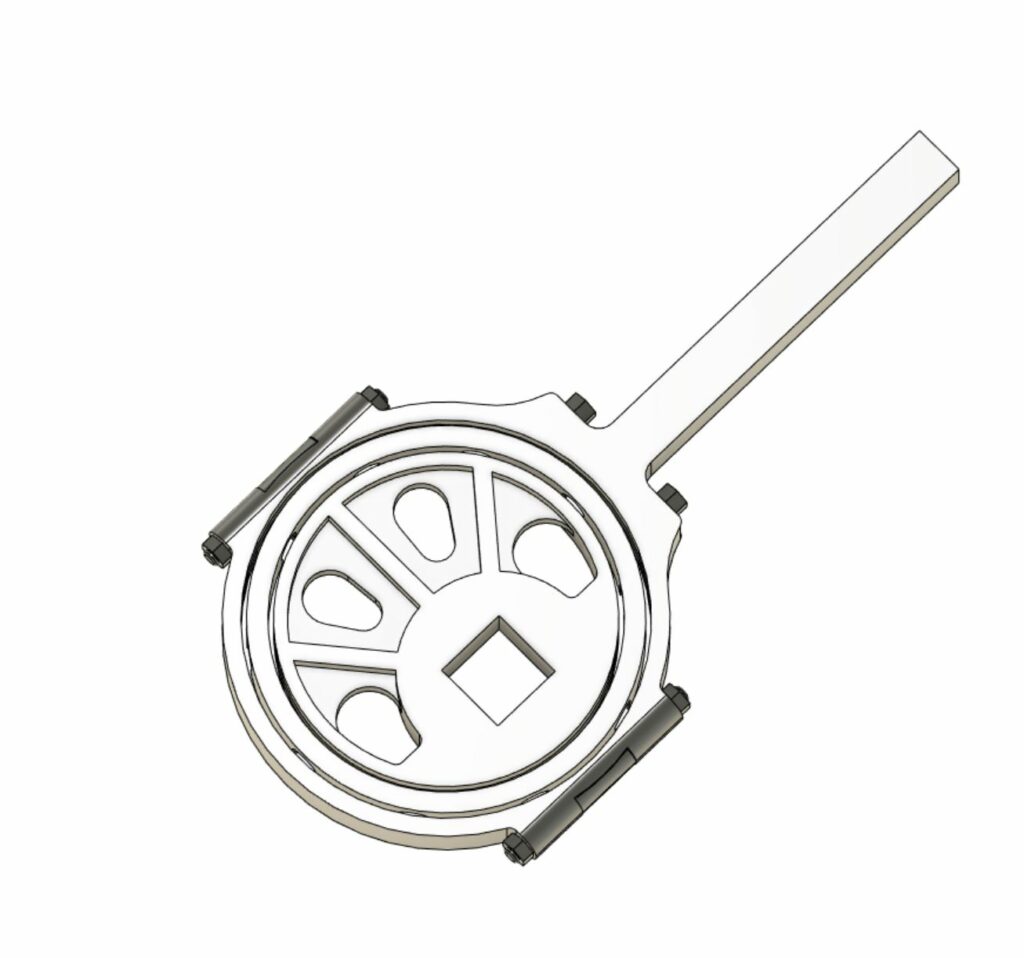
Here are some stats for this build:
Scale:
1:37.5
Size of the engine:
50 cm x 30 cm x 16 cm
Weight of the engine:
3.3 kg
Diameter propeller:
28 cm
Weight propeller:
210 g
Design time:
~300 h
Print time:
~200 h
If you also have an idea for a 3D printed machine, please do not hesitate to contact me using my email address