I moved some time ago, and one of the moving gifts was an ice cream machine. It works by crushing frozen fruits into sorbet. Quite a lot of fun to be honest. But unfortunately, after only a few servings, we found a major weak point of the maschine. The gears that are used to reduce the motor rpm to get the required strength to crush the frozen fruits are made from plastic. Especially the lower stages that turn slower and have to endure a lot of power are therefore under a lot of strain. One of these gears sheared off its teeth when some of the used fruits were probably still too hard.
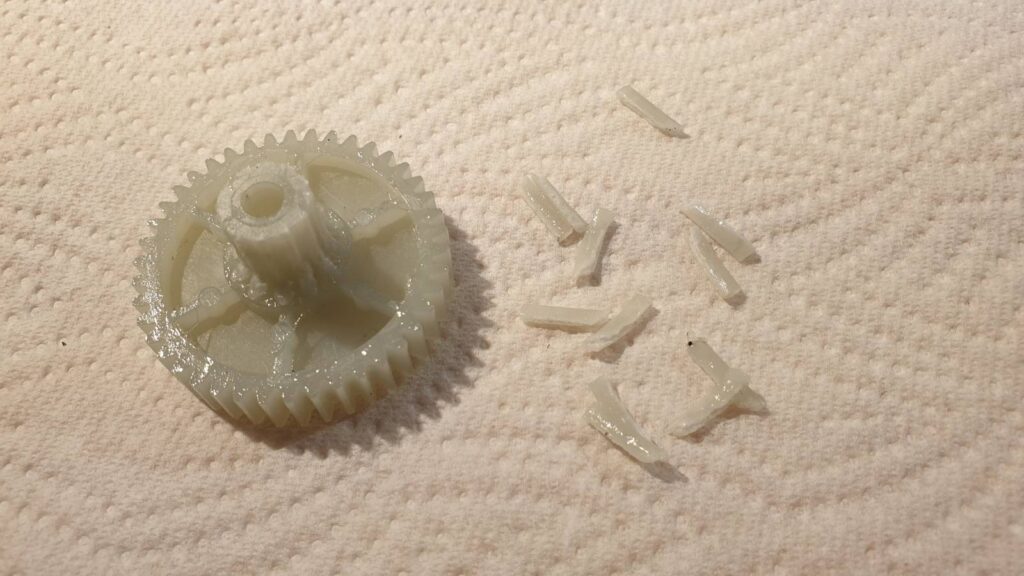
Some time spent disassembling the machine and searching online for the matching replacement gear revealed that we were out of luck and this was probably a custom made gear with no available replacement parts. If there weren’t the magic of CAD and 3D printing. After designing for a bit in Fusion360, I had recreated the exact gear. To ensure a good fit, I printed it from PETG which showed that the tolerances on the first iteration were kind of tight, but the second iteration fit like a glove.
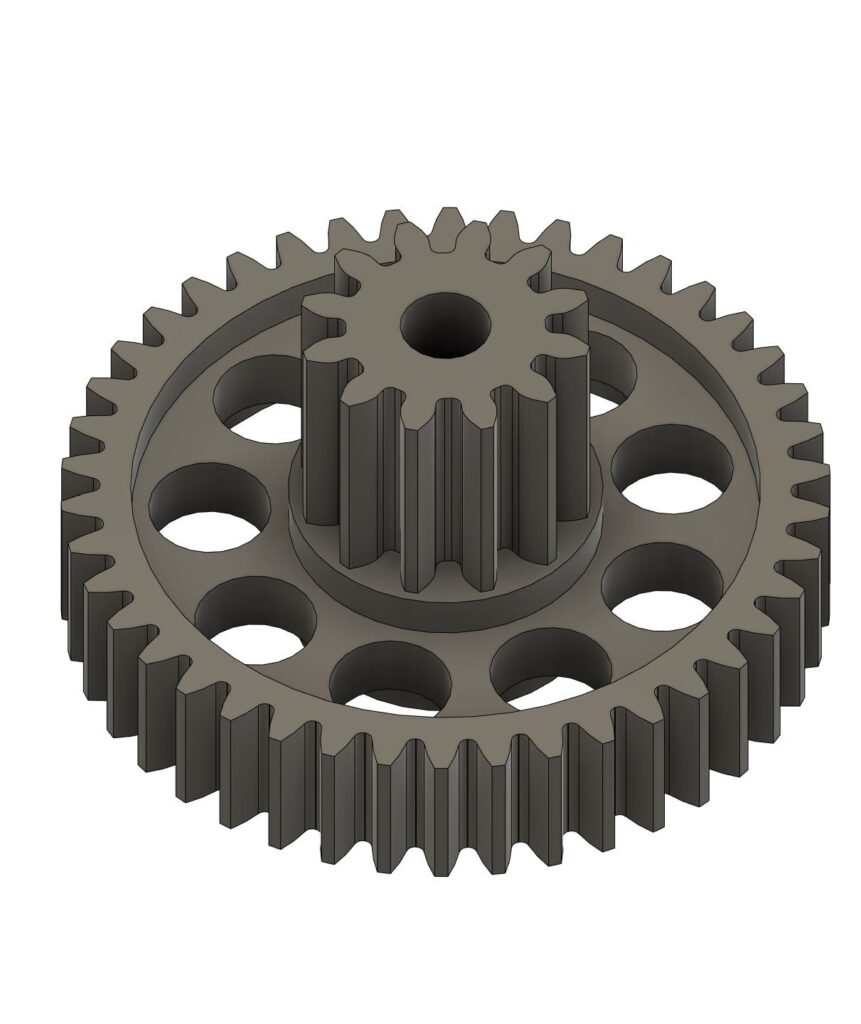
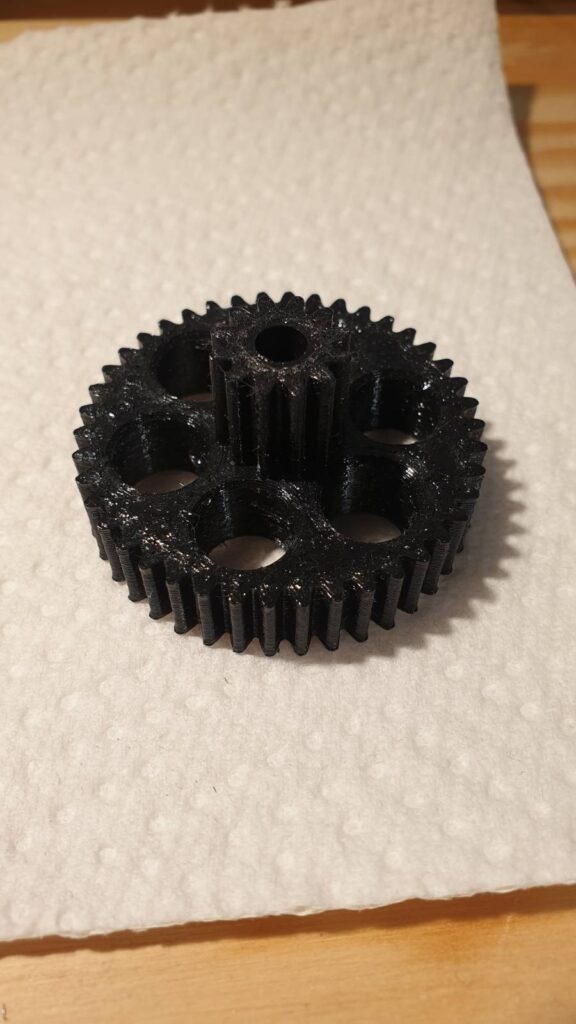
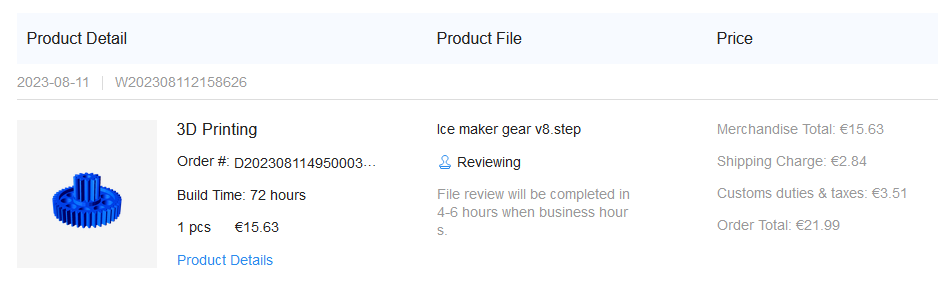
That said, I did not have a lot of trust in my 3D printed gear so I ordered the CAD model online, made from 3D printed sintered stainless steel. But since the plastic gear was already in the machine, I figured I might just use the ice maker as usual and see how much the PETG gear can take. And what can I say, the gear was working perfectly. Even so good that when the metal gear arrived I did not bother installing it because why change a winning team.
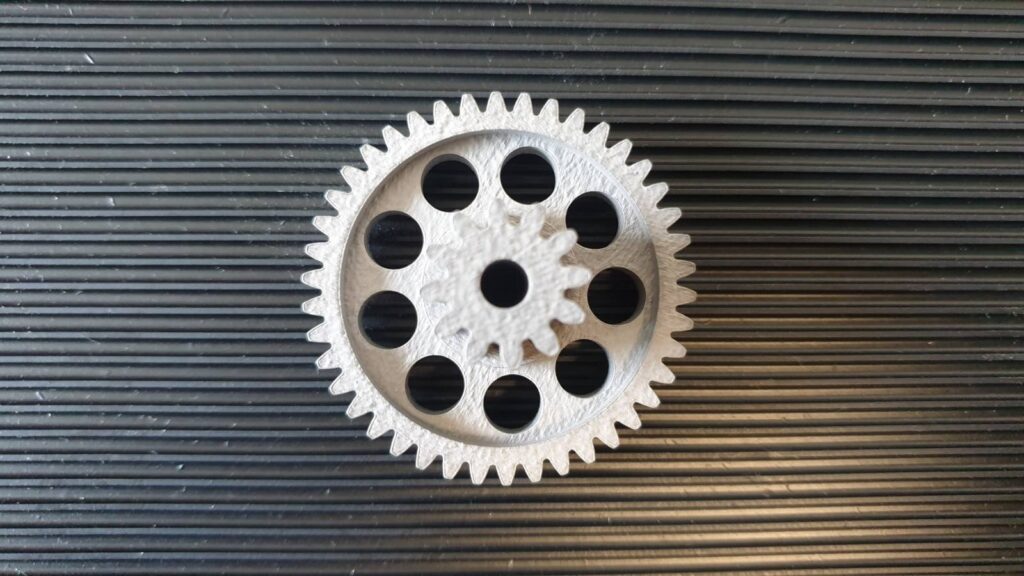
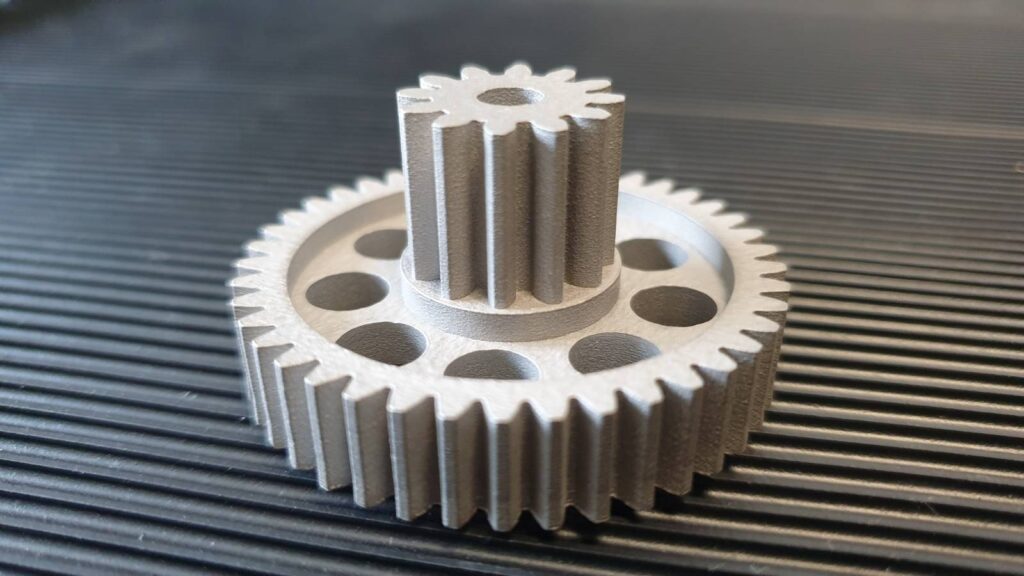
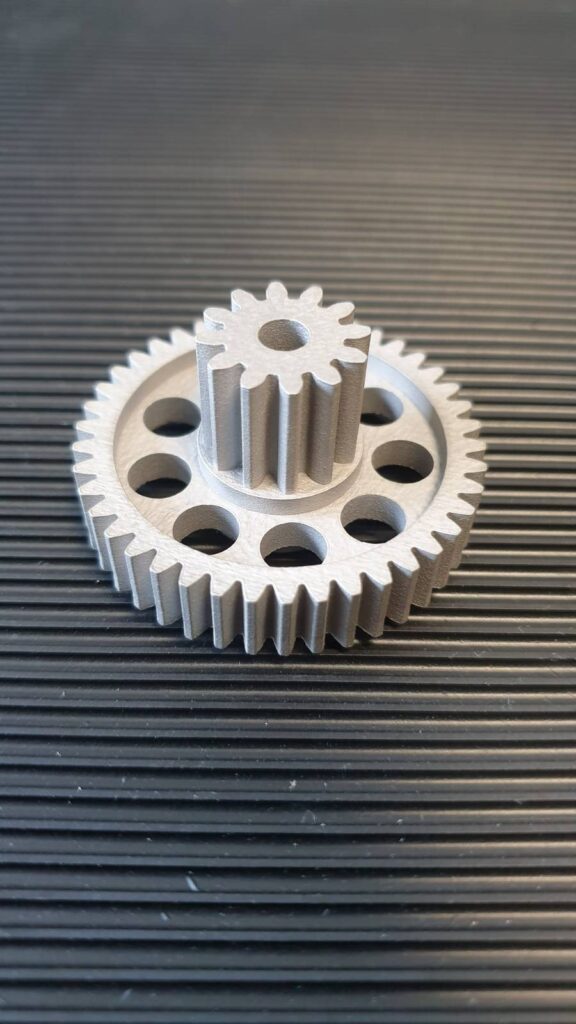
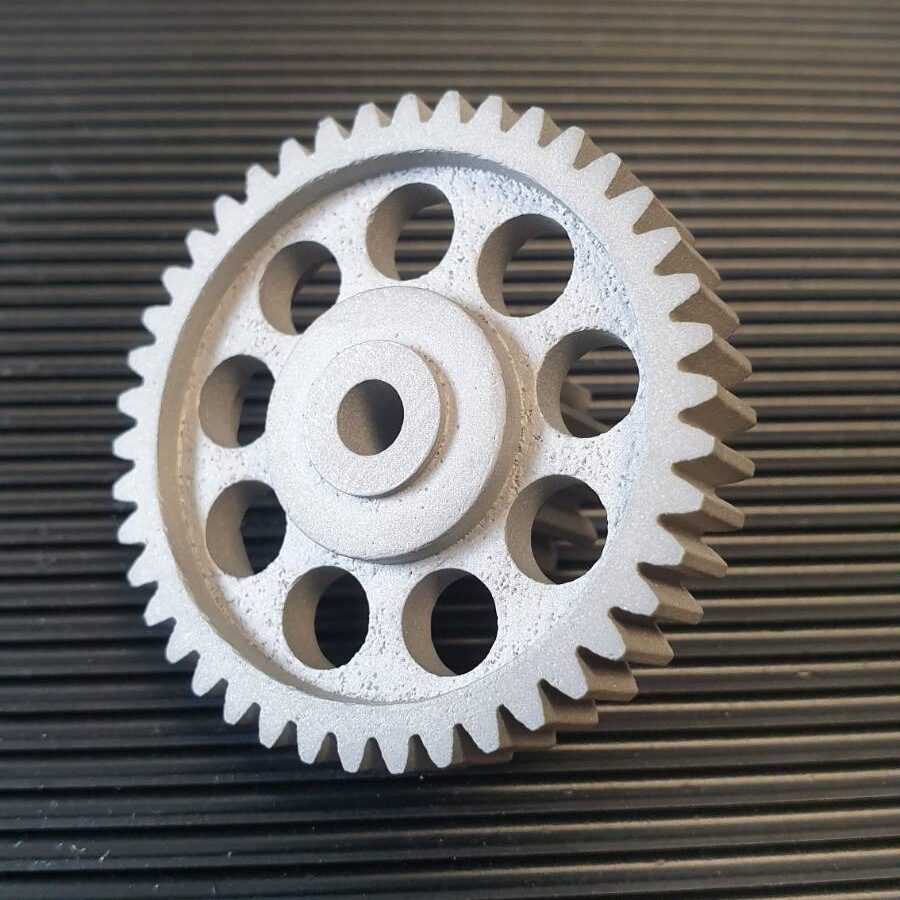
After quite a few servings of ice cream however, the PETG gear finally gave in but in a different way than I had expected. For this gear, the teeth did not shear off but the gear split along the layer lines between the smaller and the bigger gear. But the replacement was easy and the metal gear just perfectly now
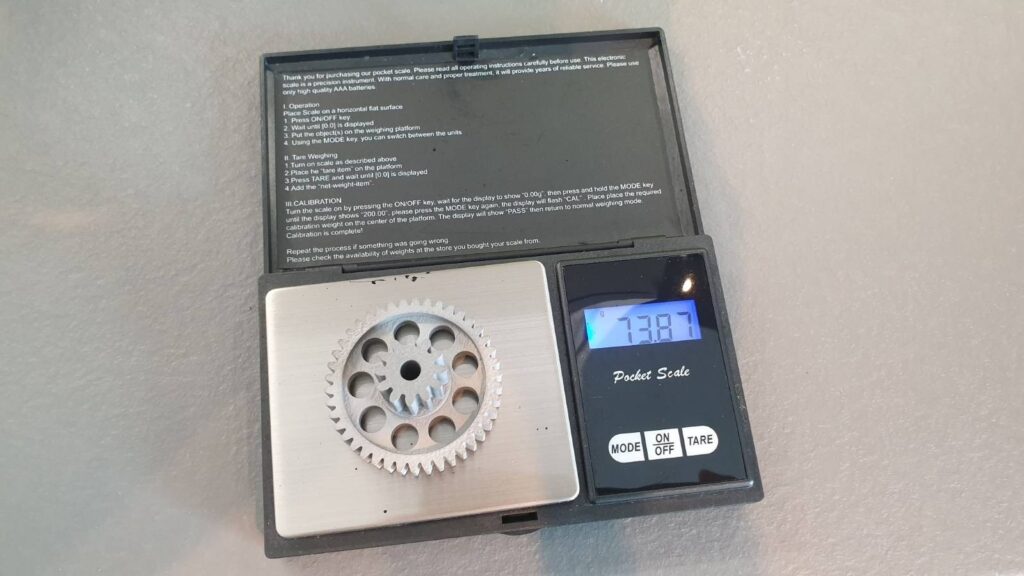
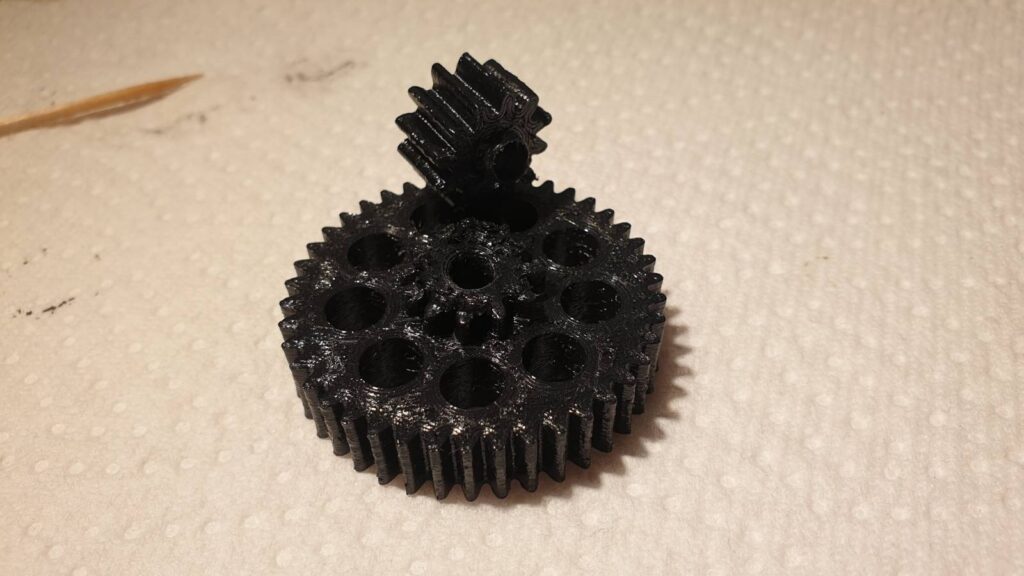
If you need a custom replacement part that is stronger than 3D printed plastic with a really intricate shape, write me an email and let’s see if we can fix another machine.